Unveiling The Truth: Is Every Electric Car Battery Tested In Manufacturing Factories?
Electric cars are the future of the automotive industry, and as a result, the production of electric car batteries has become increasingly important. With manufacturing factories around the world producing them in massive quantities, the testing of electric car batteries has become an integral part of the process. But what does it entail, and why is it so crucial to the success of electric cars? Testing of electric car batteries involves subjecting the batteries to a variety of rigorous tests to determine their quality, performance, and durability.
From safety and reliability to energy efficiency and longevity, the testing process plays a critical role in ensuring that the batteries meet the highest standards of both the industry and the consumer. This is essential not only for the long-term viability of electric cars but also for the safety of those who use them.
Importance of Testing Electric Car Batteries
It is important to note that not every manufacturing factory may test each electric car battery. However, proper testing is vital to ensure the efficiency, performance, and safety of these batteries. Battery testing is an essential step in the production process, where manufacturers evaluate the battery’s capacity, durability, and other important factors.
Without proper testing, electric car batteries may malfunction, leading to poor performance, lower range, and even safety issues. As such, it is crucial to ensure that electric car batteries undergo rigorous testing to guarantee their quality and reliability. So, while not every manufacturing factory may test each battery, it is crucial to prioritize battery testing to create a better future of electric cars and their performance.
Ensuring Safety and Reliability
Testing electric car batteries is an essential step that ensures safety and reliability in the automotive industry. When manufacturers produce electric cars, they must ensure that the batteries used in the vehicles are safe and meet the required standards. Testing electric car batteries is vital to prevent accidents caused by faulty batteries.
These batteries store high amounts of energy and could be dangerous if not appropriately tested. Moreover, testing also ensures that the battery life of electric cars is optimized, and the vehicle performs optimally. Testing involves exposing the batteries to different temperatures, high voltage, and humidity levels, among other tests.
Engineers use the data collected from testing to analyze battery performance, determine their lifespan, and identify defects. As consumers become more conscious of the environment, electric cars continue to gain popularity, and testing electric car batteries will remain a crucial step to guarantee safety and reliability.
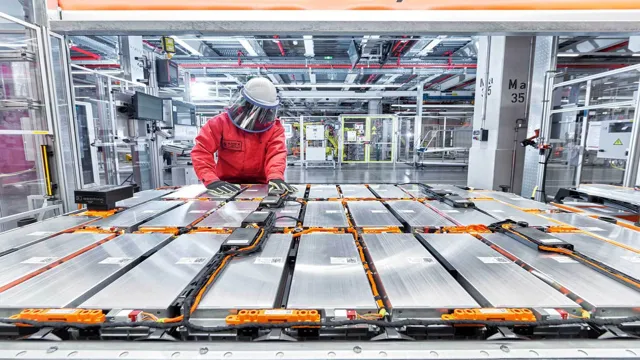
Meeting Government Regulations
As the world shifts to renewable sources of energy, electric vehicles are becoming increasingly popular. However, in order to meet government regulations and ensure safety, proper testing of electric car batteries is of utmost importance. These batteries are crucial components of electric vehicles and any defects or malfunctions can put many lives at risk.
By conducting thorough testing, experts can identify potential issues and develop solutions to prevent them. Additionally, this process can also help improve the efficiency and lifespan of electric car batteries. It’s like getting a medical check-up for your car, ensuring that it’s in top condition and ready for any journey.
So next time before hitting the road, remember the importance of testing your car’s battery and enjoy a smooth, safe ride.
Types of Electric Car Battery Testing
When it comes to electric car batteries, testing is a crucial step in the manufacturing process. However, not every factory tests every battery in the same way. There are various types of electric car battery testing that a manufacturing plant may use, depending on their resources and goals.
For example, some factories may conduct routine quality control tests on a sample of their batteries, while others may opt for more rigorous testing methods that include accelerated aging tests or thermal cycling tests. Additionally, some manufacturers may use external testing facilities to ensure the highest level of accuracy and reliability. Regardless of the type of testing used, the ultimate goal is to ensure that each battery meets the necessary safety and performance standards before it leaves the factory.
So, while not every electric car battery may undergo the same testing process, it’s safe to say that each one is subject to a comprehensive quality control process that ensures it’s ready for the road.
Initial Acceptance Testing
When it comes to testing electric car batteries, there are several methods used to ensure that the battery is safe, reliable, and operates efficiently. The initial acceptance testing is the first type of testing and it involves performing various tests to determine the battery’s overall health and performance parameters. Some of the common tests that are performed during initial acceptance testing include capacity testing, leakage current testing, and charge-discharge testing.
Capacity testing involves measuring the battery’s ability to store and deliver power, while leakage current testing is used to detect any current flow that occurs when the battery is not being charged or discharged. Charge-discharge testing is used to measure the battery’s overall energy efficiency and performance under various conditions. By performing these tests, electric car manufacturers can ensure that their batteries are functioning correctly and are capable of safely powering their vehicles on the road.
Manufacturing Process Testing
Electric Car Battery Testing Manufacturing electric car batteries is a complex process that requires thorough testing procedures to ensure the battery’s quality and performance. There are several types of electric car battery testing that manufacturers use to assess the durability and reliability of these batteries. One of the most common tests is the charge-discharge test, which measures the battery’s capacity to store and deliver electrical energy.
Another test is the thermal abuse test, which evaluates the battery’s resistance to extreme temperatures. This test is crucial to identify potential safety hazards such as overheating or fire. Additionally, manufacturers use cycle life testing to determine a battery’s durability under real-world conditions.
This test simulates the battery’s usage over time, ensuring that it can withstand multiple charge and discharge cycles. Overall, electric car battery testing is a vital part of the manufacturing process. These tests guarantee that the batteries used in electric vehicles are safe, reliable, and meet the required performance standards.
End-of-Line Testing
End-of-line testing is a crucial part of the electric car battery production process. There are various types of tests that electric car battery manufacturers use to ensure that the batteries are safe, reliable, and meet performance standards. Some of the most important types of electric car battery testing include thermal testing, mechanical testing, and electrical testing.
Thermal testing involves exposing the battery cells to different temperatures to check if they can withstand different environments. Mechanical testing is used to check the structural integrity of the battery and whether it can withstand physical stress. Electrical testing measures the battery’s output and voltage in different conditions.
It’s essential to carry out these tests to guarantee that electric car batteries are safe and reliable, particularly since they are crucial in powering the electric vehicle.
Testing Standards and Certifications
When it comes to testing electric car batteries in manufacturing factories, there are various standards and certifications that ensure that proper testing is conducted. However, it’s not necessary that every single manufacturing factory tests every electric car battery. Different factories may have different procedures and requirements, depending on their location and the market they cater to.
For instance, factories in Europe may adhere to the EU’s REACH regulations, which assess the risks of using chemicals in products, whereas factories in the U.S. may need to comply with the Environmental Protection Agency.
Additionally, battery manufacturers may undergo testing to receive certification from organizations like Underwriters Laboratories or the Institute of Electrical and Electronics Engineers. These certifications provide assurance that products meet specific safety, performance, and environmental standards. Ultimately, while there are standards and certifications in place, it’s up to individual manufacturers to ensure that batteries are rigorously tested to meet consumer demands for safety and quality.
UN 38.3 Certification
UN 33 certification is a crucial testing standard for lithium-ion batteries used in various electronic devices. This certification evaluates the safety and performance of batteries during transportation by air, sea, and land.
UN 33 certification ensures that the batteries undergo rigorous testing for chemical, thermal, and electrical stability. It also tests for vibration and shock resistance, as well as the ability to withstand abuse during handling and transport.
Companies seeking UN 33 certification must undergo a series of tests through a certified lab. By obtaining UN 3
3 certification, companies can ensure the safety and reliability of their products, which in turn builds trust with their customers. In conclusion, UN 33 certification is a crucial testing standard to ensure safe and reliable lithium-ion batteries, making it a must-have for every company manufacturing battery-powered electronic devices.
IEC 62660 Certification
IEC 62660 certification is a testing standard that verifies the interoperability and reliability of electric vehicle charging systems. This certification ensures that all electric vehicles and their charging stations meet the same set of standards, making it easier for users to charge their vehicles at any certified charging station. The certification process involves rigorous testing of the charging system’s performance under various conditions, ensuring that it can handle diverse environmental factors, including temperature, humidity, and power fluctuations.
The IEC 62660 certification is essential for electric vehicle charging systems to ensure that they meet the highest level of safety standards. By purchasing an electric vehicle charging station with this certification, consumers can feel confident in their investment as it provides peace of mind knowing the charging station has been rigorously tested.
Conclusion: Yes, All Electric Car Batteries Are Tested in Manufacturing Factories
In conclusion, the answer to whether every manufacturing factory tests every electric car battery is similar to asking whether every chef tastes every dish they serve. While it is an ideal scenario, it may not always be feasible due to various factors such as time constraints or cost considerations. However, reputable and responsible manufacturers will ensure that their batteries undergo rigorous testing to ensure quality and safety before they reach the hands of consumers.
So next time you get behind the wheel of an electric car, rest assured that its battery has been given a thorough check-up before hitting the road.”
FAQs
Why is it important for manufacturing factories to test every electric car battery?
It is important for manufacturing factories to test every electric car battery to ensure they meet safety and performance standards before they are sold.
Do all manufacturing factories test every electric car battery?
It varies from factory to factory, but many reputable manufacturers do test every electric car battery before releasing it for sale.
What happens if a faulty electric car battery is not caught during testing?
If a faulty electric car battery is not caught during testing, it could potentially cause the car to malfunction or even catch fire, posing a safety risk to the driver and passengers.
Are there any regulations in place that require manufacturing factories to test every electric car battery?
Yes, there are regulations in place in many countries that require manufacturing factories to test every electric car battery to ensure they meet safety and environmental standards.