Rev Up Your Ride: A Comprehensive Guide to DIY Electric Car Lithium Battery Conversion
Have you heard about the DIY electric car trend that’s taking over the automotive world? It’s no secret that electric cars are the future of transportation, but did you know you can build your own electric vehicle with lithium batteries? That’s right, by using high-performance lithium batteries and following a few simple steps, you can build an environmentally friendly car that’s both cost-effective and efficient. Lithium batteries are becoming increasingly popular in the electric car industry. Their high energy capacity and long lifespan make them the ideal power source for electric vehicles.
With the rising demand for electric cars and the increasing cost of fossil fuels, building your own electric car with lithium batteries could be the perfect solution to your transportation needs. But where do you start? Don’t worry, we’ve got you covered. In this blog, we’ll guide you through the process of building your own electric car with lithium batteries.
We’ll go over everything from choosing the right batteries to wiring up your car’s electrical system. By the end of this blog, you’ll have all the knowledge you need to build your very own DIY electric car. So, whether you’re a seasoned DIYer or a beginner looking to get into the world of electric cars, this blog is for you.
Buckle up, and let’s get started!
Why Lithium-Ion Batteries?
If you’re considering building a DIY electric car, one of the most critical components you’ll need are lithium-ion batteries. These batteries have become the go-to choice for electric cars, as they’re lighter, more energy-dense, and longer-lasting than other battery types. Lithium-ion batteries can store more energy in a smaller space, which is crucial for electric vehicles that need to maximize their range.
Additionally, they’re more resistant to “memory effect,” which occurs when a battery becomes less efficient over time due to repeated charging and discharging. Lithium-ion batteries are also safer, as they’re less likely to overheat or catch fire than older battery technologies. While they may be more expensive upfront, the long-term cost savings and environmental benefits make them an excellent choice for those looking to build an electric car.
So, if you’re considering a DIY electric car project, make sure you do your research and invest in lithium-ion batteries to ensure optimal performance and safety.
Advantages over Other Battery Types
Lithium-ion batteries are becoming increasingly popular in various industries due to their numerous advantages over other types of batteries. Firstly, they offer a higher energy density, which means they can store more energy compared to other batteries of the same size. This makes them ideal for use in portable devices and electric vehicles that require long-lasting power.
Secondly, lithium-ion batteries have a longer lifespan than other battery types, meaning they can be recharged and used over and over again. Thirdly, they have a low self-discharge rate, which means they can retain their charge for longer periods of time without needing a recharge. Another great advantage is that lithium-ion batteries are lightweight and small, making them easy to transport and install in various applications.
Overall, lithium-ion batteries offer a reliable and efficient power source with a longer lifespan and higher energy density than other types, making them a popular choice for a variety of applications.
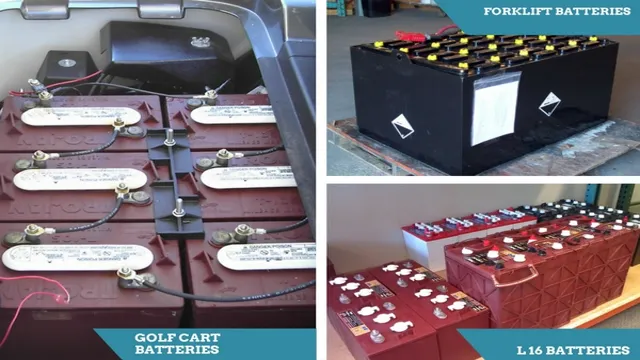
Longer Lifespan and Higher Energy Density
Lithium-ion batteries have become increasingly popular due to their longer lifespan and higher energy density. Compared to older battery models, lithium-ion batteries can hold more energy and last longer before needing to be replaced. This is due to the use of lithium ions that move back and forth between electrodes to create a charge, rather than the acidic chemical reactions found in older batteries.
Additionally, lithium-ion batteries have become more cost-effective to manufacture, making them an ideal choice for many different applications. These batteries are commonly found in electronic devices such as smartphones, laptops, and tablets, but they are also used in electric vehicles and renewable energy storage systems. The benefits of utilizing lithium-ion batteries are clear as they provide long-lasting, efficient power that is critical to modern technology.
Calculating Battery Needs
When it comes to DIY electric cars, choosing the right type of lithium battery for your vehicle can be a daunting task. The first thing you need to determine is how much power your car needs. One way to calculate this is by figuring out the maximum wattage your car’s motor will draw during normal operation and multiplying this by the number of hours you plan to run the car before recharging.
This will give you the total watt-hours needed for your battery. Once you know this number, you will need to choose a battery with enough capacity to provide this power to your motor. Keep in mind that lithium batteries come in different configurations, and the number of cells and the voltage rating will affect the energy capacity of your battery system.
Additionally, it’s important to take into consideration a safety buffer to ensure the longevity and stability of your battery pack, as uncalculated battery systems can lead to disastrous results. Ultimately, choosing the right lithium battery system for your DIY electric car requires careful planning, research, and calculations. But with a little patience and effort, you can create an efficient and reliable electric vehicle that meets your needs.
Determining Voltage and Capacity Requirements
When it comes to determining the voltage and capacity requirements for your battery needs, there are a few things you should consider. First, take a look at the devices you plan to power and check their voltage requirements. You will need a battery with a voltage that matches or slightly exceeds the device’s requirements.
Next, think about the capacity you will need. This is determined by the amount of energy your devices consume over time. If your devices require a lot of power, you will need a larger capacity battery to avoid frequent recharging.
To calculate the capacity you need, you can multiply the device’s wattage rating by the amount of time you plan to use it. Finally, consider the type of battery you need – whether it’s a lithium-ion, nickel-cadmium, or another type based on your specific use case. By considering all of these factors, you can ensure that your battery matches your needs and will provide reliable power to your devices.
Matching Cells with BMS
When it comes to calculating battery needs for a Battery Management System (BMS), it’s crucial to match the cells properly. This means ensuring that the cells have the same specifications in terms of voltage, capacity, and chemistry. Matching cells is important because it helps to maintain balance and maximize the overall performance of the battery.
To calculate the battery needs for a BMS, you’ll need to start by determining how much power is required for your specific application, as well as the voltage and total capacity required. Once you have this information, you can then decide on the number and size of cells needed to meet these requirements. It’s important to keep in mind that using mismatched cells or not having enough cells can result in poor performance and potentially even dangerous situations.
Overall, calculating battery needs for a BMS is a vital process that requires careful planning and consideration. By matching cells correctly and taking into account all necessary factors, you can create a battery system that delivers optimal performance and meets your specific needs.
Choosing and Sourcing Components
When it comes to DIY electric car lithium batteries, choosing and sourcing the right components can be a challenging task. One of the most crucial components of an electric car battery is the lithium-ion cells. These cells come in various shapes and sizes, and each has its own advantages and disadvantages.
The two most commonly used lithium-ion cells are cylindrical and pouch cells. Cylindrical cells are more durable and have a longer lifespan, while pouch cells are lighter and offer greater flexibility in terms of shape and size. Other components that need to be considered when building a lithium-ion battery for an electric car include the battery management system (BMS), charger, and cooling system.
It is essential to choose high-quality components that are compatible with each other and also meet safety standards. Sourcing these components from reliable suppliers who offer warranties and technical support is also important for the success of the DIY project. With the right components and proper planning, building a lithium-ion battery for your electric car can be a rewarding and fulfilling experience that also ensures a greener future.
Reliable Suppliers for Lithium Cells and BMSs
When it comes to building a lithium battery pack, choosing reliable suppliers for cells and battery management systems (BMSs) is crucial. You want to make sure you are sourcing high-quality components that will perform well and last a long time. There are a few things to consider when choosing a supplier, such as the capacity and specifications of the cells, the reputation of the supplier, and the availability of technical support.
Some reputable suppliers of lithium cells include Panasonic, LG, Samsung, and Sony. For BMSs, companies like Orion BMS and Ewert Energy Systems are well-known for their quality and reliability. It’s also important to consider the price of the components, as cheaper options may not always be the best choice.
Ultimately, it’s worth investing in high-quality components to ensure a safe and reliable battery pack.
Balancing and Protection Circuitry
When it comes to balancing and protection circuitry for your project, choosing the right components can make all the difference. One key component to consider is the battery protection circuit board. This board helps protect your battery from overcharging, over-discharging, and overcurrent situations.
It can also help balance the voltage of individual battery cells, ensuring that they all discharge and charge evenly. Another important component is the current sense resistor, which measures the current flowing through your battery and helps protect against short circuits and other potential hazards. Capacitors are also commonly used in battery protection circuits to help smooth out voltage spikes and protect against sudden power surges.
When selecting these components, it’s important to ensure that they are compatible with your battery chemistry and voltage requirements. With the right components in place, you can help ensure that your battery operates safely and efficiently.
Building and Testing Your Battery Pack
DIY electric car enthusiasts often aim to build their own lithium battery packs. While this can be a rewarding and cost-effective way to power your electric vehicle, it’s crucial to properly plan and test your battery pack before installing it into your car. Firstly, it’s important to decide what type of lithium cells you want to use, as well as their voltage and capacity.
Then, you’ll need to assemble the cells in a manner that distributes the load evenly while keeping the overall weight and size manageable. Once assembled, testing the battery pack is critical to ensure safety and efficiency. This includes checking for cell imbalances, verifying the wiring and connections, and measuring the overall capacity and range of the battery pack.
Proper planning and testing of your DIY lithium batteries is essential to a safe and successful electric car conversion.
Cell Configuration and Pack Assembly
Building and testing a battery pack can seem overwhelming, but with the right knowledge, it can be a smooth process. The first step is to plan out the cell configuration. This involves deciding on the number of cells and how they will be wired together.
It’s important to consider factors such as voltage and capacity when deciding on a configuration. Once the configuration is determined, it’s time to assemble the pack. This involves soldering the cells together and insulating them properly.
It’s important to be careful during this process to avoid damaging the cells or creating a short circuit. After the pack is assembled, it’s time to test it. This involves using a multimeter to measure the voltage and ensuring that all of the cells are properly balanced.
It’s also important to perform a discharge test to determine the capacity of the pack. This test involves discharging the pack at a specific rate and measuring the time it takes for the voltage to drop to a certain level. Building and testing a battery pack may seem intimidating, but with the right knowledge and care, it can be a successful project.
It’s important to always prioritize safety and to double-check all connections before testing the pack. By following these steps, you can ensure that your battery pack is reliable and ready to power your project.
Testing and Calibration Procedures
When it comes to building a battery pack, the testing and calibration procedures play a crucial role in ensuring that it performs as expected. Before you start putting your battery pack together, it’s essential to test each individual battery cell to ensure they’re all fully charged and have the same voltage. Once you’ve assembled your battery pack, it’s time to run a series of performance tests to determine its capacity and discharge rate.
This involves discharging the battery pack at a specific rate and measuring the time it takes to discharge fully. If you’re happy with the results, you can move onto the calibration stage, where you adjust the voltage output to match your device’s specifications. Overall, it’s essential to take your time and carefully follow each step of the testing and calibration procedures to ensure your battery pack performs safely and reliably.
Conclusion
As we’ve seen, building a DIY electric car powered by lithium batteries is a challenging but rewarding endeavor. With careful planning and attention to detail, it’s possible to create a vehicle that is both efficient and environmentally friendly. So why not join the growing community of electric car enthusiasts and take control of your driving experience? With a little bit of know-how and a lot of determination, the road to the future is yours to create!”
FAQs
What are the advantages of using lithium batteries in a DIY electric car?
Lithium batteries have a higher energy density, longer lifespan, and lower weight compared to traditional lead-acid batteries, making them a more efficient and practical choice for powering a DIY electric car.
Can any type of lithium battery be used in a DIY electric car?
No, only certain types of lithium batteries, such as Lithium Iron Phosphate (LiFePO4) or Lithium Nickel Cobalt Aluminum Oxide (NCA), are suitable for use in a DIY electric car due to their ability to handle high discharge rates and provide consistent power output.
How do I properly install and maintain lithium batteries in my DIY electric car?
Proper installation and maintenance of lithium batteries in a DIY electric car involve ensuring proper wiring, securing the batteries in place, monitoring their temperature and charge levels, and using a Battery Management System (BMS) to prevent overcharging or discharging.
How do lithium batteries compare to other types of batteries in terms of cost and availability?
While lithium batteries may be more expensive upfront, their longer lifespan and higher efficiency can lead to cost savings in the long run. Additionally, the increasing demand for electric vehicles and renewable energy storage has led to a growing availability of lithium batteries on the market.