Revolutionizing the Future: Unveiling the Electric Car Battery Production Process
Have you ever thought about how the batteries for electric vehicles are made? It’s a fascinating process that involves a mixture of advanced technology and careful engineering. The production of electric car batteries has come a long way since the first electric cars were born, with the process now being more efficient and eco-friendly than ever before. In this blog post, we’ll explore the ins and outs of electric car battery production, from the first stage of raw material sourcing to the final assembly of the battery pack.
So, buckle up and get ready to delve into the world of electric car batteries!
Overview of Battery Production
The electric car battery production process is a complex and highly technical procedure that involves several stages. The process typically begins with the production of raw materials that are used in the making of the batteries, including lithium, cobalt, nickel, and other materials. These materials are then refined into their respective chemical forms and processed into battery components.
Once all the necessary battery components have been manufactured, they are assembled into the final battery pack, which is then tested for quality and performance. The battery production process is highly regulated to ensure the highest standards of safety and performance. Despite the challenges involved in producing electric car batteries, the industry is constantly innovating and improving its processes to meet the growing demand for sustainable transportation.
Raw Materials and Quality Control
Battery production requires various raw materials such as cathodes, anodes, separators, electrolytes, and an array of other components. The quality of these raw materials is critical as it directly impacts the performance, reliability, and safety of the batteries. For instance, the purity of cathode materials determines the energy density, whereas the quality of electrolytes influences the battery’s lifespan and temperature resistance.
Therefore, manufacturers must use high-quality raw materials from trustworthy suppliers and perform strict quality control procedures to ensure consistent production. These measures involve monitoring the chemical composition, particle size, morphology, and other physical and chemical properties necessary to meet the battery’s specifications. The production process must also comply with regulatory standards and guidelines for safety and environmental protection, such as using non-toxic and recyclable materials.
In essence, the success of battery production largely depends on the quality of raw materials and rigorous quality control practices.
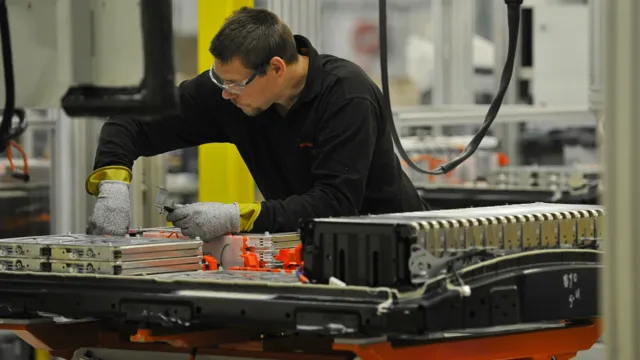
Preparation of Battery Components
Battery production is a complex process that involves the preparation of various components to ensure the efficient functioning of the battery. The production process begins with the preparation of electrode materials, which are the key components of the battery. This involves mixing active material, conductive additives, and a binder to form a homogeneous mixture.
The mixture is then coated onto a current collector and dried to produce the electrode plate. A separator, which is an insulating layer, is placed between the electrode plates to prevent them from touching each other. The next step involves winding the electrode plates and separator into a cylindrical shape and placing them in a container.
A conductive electrolyte is then added to the container to facilitate the movement of ions between the electrodes, and the container is sealed to prevent leakage. Battery production involves a variety of complex processes that require attention to detail to ensure the quality and efficiency of the final product.
Assembly of Battery Cells
Assembling battery cells is a crucial step in the electric car battery production process. This is where individual cells are connected to make a complete battery pack. The process involves placing the lithium-ion cells, which have been tested and sorted into batches based on their capacity and performance, into a protective housing.
The cells are then wired together in a particular pattern, usually in series, to achieve the desired voltage output. The interconnection process is automated to ensure consistency and precision, with robots performing the task of connecting the cells with high accuracy. The final product is a complete battery pack with a specific voltage and energy capacity that is essential in powering the electric motor of an electric vehicle.
The efficiency and reliability of the battery pack significantly depend on the quality of the cells and the precision of their interconnection, making the assembly process a crucial step in the electric car battery production process.
Cell Stacking and Folding
Cell stacking and folding are essential steps in the assembly of battery cells, and they play a crucial role in determining the final performance of the battery. This process involves arranging the individual cells in a particular pattern to optimize their energy and power capacity. Cell stacking involves aligning the positive and negative electrodes of the cells, while cell folding requires bending the cells to fit into the desired form factor.
Both processes require high precision and expert craftsmanship to ensure the cells are connected securely and efficiently. The outcome of cell stacking and folding determines the overall durability and reliability of the battery pack. Therefore, it is vital to work with experienced battery manufacturers who have the expertise to assemble the battery cells with the highest level of accuracy and quality.
With the right expertise, the final product will be a high-performance and long-lasting battery pack that meets the unique requirements of the application.
Adding Electrolytes and Sealing
Assembling battery cells is a crucial step in creating a functional battery. Adding electrolytes and sealing the cells are important aspects of this process. Electrolytes are the conductive solution that allows for the flow of ions between the cathode and anode.
These electrolytes can be added through different methods, such as filling the cells with the solution or injecting it into the cells. Once the cells have been filled with the electrolyte solution, they must be sealed to prevent any leakage or contamination. This sealing process involves using a sealant or adhesive to secure the top and bottom of each cell.
It is important to ensure that the sealing is done properly to avoid any issues with the battery’s performance or safety. Overall, the process of adding electrolytes and sealing the cells is a critical step in assembling battery cells and creating a functional battery.
Formation and Testing of Battery Cells
When it comes to assembling battery cells, manufacturers must follow certain steps to ensure the cells are safe and efficient. First, the cells must be tested for any defects or abnormalities. Then, the cells are sorted based on their capacity and internal resistance.
After sorting, the cells are aligned and connected with the appropriate terminals. The cells are then inserted into a container, usually made of plastic or metal, and sealed with a heat-resistant glue. This casing protects the cells from damage and prevents any leakage of electrolyte.
Finally, the assembled battery undergoes a series of tests to ensure it meets the necessary safety and functional standards before it is ready to be used. Each step of the assembly process is crucial to producing a high-quality and reliable battery cell.
Packaging and Integration
The electric car battery production process involves several critical stages, including packaging and integration. After the battery cells are manufactured, they need to be assembled into modules, which can then be combined to form a complete battery pack. This process requires precise engineering and a thorough understanding of the electrical and thermal properties of the individual cells and the overall system.
Packaging and integration also involve the design and fabrication of the enclosure that houses the battery pack. This enclosure must be thermally and electrically insulated to prevent damage to the cells and ensure safe operation of the vehicle. In addition, it must be lightweight and compact to maximize the vehicle’s range while minimizing its weight and size.
Finally, integrating the battery pack with the rest of the vehicle’s electrical system requires careful planning and execution to ensure that all components function optimally and that the vehicle can be operated safely and efficiently. Overall, the packaging and integration stage of electric car battery production plays a critical role in the performance and safety of the vehicle, with each step requiring careful attention to detail and a deep understanding of the underlying technology.
Module and Pack Assembly
When it comes to the production of electronic devices, packaging and integration are crucial components that should not be overlooked. Module and pack assembly make up the process of packaging and integration, which involves fitting various parts together to create a functional device. It involves bringing together different components such as printed circuit boards (PCBs), integrated circuits (ICs), connectors, and cables to form an electronic package that meets specific requirements.
This process involves ensuring that the modules and packs are assembled accurately, in the right sequence, and in line with industry standards. The goal is to create electronic devices that are reliable, compact, and efficient while reducing production costs and improving performance. Manufacturers who understand the complexities of module and pack assembly see benefits that include higher production rates, reduced errors, and lower production costs.
Testing and Inspection
Packaging and Integration Testing and Inspection are crucial stages in the manufacturing process. Packaging testing ensures that the packaging material is fit for purpose and that the product is protected during transportation and storage. The tests can vary from shock and vibration tests, moisture tests to compression tests, and drop tests.
Packaging testing is important because it can help prevent damages, reduce costs, and enhance customer satisfaction. Integration testing, on the other hand, involves testing the system as a whole to ensure that all the components have been integrated correctly and are functioning as expected. This ensures that the system is ready to be deployed and can operate seamlessly.
Integration testing ensures that there are no defects or errors that can compromise system performance, quality, or reliability. By testing and inspecting the packaging and integration system, manufacturers can deliver a high-quality product that meets the customer’s expectations.
Final Thoughts
In conclusion, the electric car battery production process is a complex and crucial aspect of the electric car industry. It involves a series of steps, including cell manufacturing, module assembly, and pack assembly, where various components are carefully pieced together to create a functioning battery. The process requires sophisticated technology and equipment along with skilled workers to ensure precision and consistency.
As the demand for electric cars rises, the production process must keep pace to avoid supply chain disruptions. The development of sustainable and eco-friendly production methods is also critical to ensuring that the production process does not compromise the environment. Overall, the electric car battery production process is a fascinating and intricate process that is key to the growth and success of the electric car industry.
Conclusion
In conclusion, the process of producing electric car batteries is a complex and energy-intensive endeavor. But the end result is worth it – a vehicle that’s kinder to the environment, better for your wallet, and sure to spark envy in even the most dedicated gas-guzzling gearheads. So the next time you see an electric car cruising down the road, remember the effort, science, and ingenuity that went into powering it, and feel confident that you’re making the right choice for the planet and your pocketbook.
“
FAQs
What is the process for manufacturing electric car batteries?
The production process includes mixing raw materials, creating cells, assembling modules, and testing for quality control.
How does the battery pack work in an electric car?
The battery pack stores electrical energy that powers the electric motor, which propels the car forward.
What raw materials are used in electric car battery production?
Common materials include lithium, cobalt, nickel, graphite, aluminum, and copper.
How long does it take to produce a single electric car battery?
The time it takes to produce a battery varies depending on the manufacturer and the size of the battery. It can take anywhere from a few hours to several days.