Unveiling the Mystery Behind Internal Liquid Outlet Valve – Everything You Need to Know!
If you have ever wondered how liquid dispensers work, you may be curious about what the internal liquid outlet valve does. This tiny valve, often found inside dispensing equipment, plays a crucial role in allowing for precise and controlled flow of liquid from the container to the recipient. Think of it like the faucet for your sink – it regulates the flow of water so that it comes out at just the right pace and volume.
Without a functioning internal liquid outlet valve, dispensers could leak, dispense too quickly, or fail to work altogether. Whether you’re looking to buy or repair a dispensing system, understanding the role of the internal liquid outlet valve can help you make more informed decisions. In this blog post, we’ll dive into the specifics of what this valve does, how it works, and why it matters for your dispensing needs.
Get ready to become a liquid-dispensing expert!
Function
The internal liquid outlet valve is an essential component of many types of machinery that require liquid transfer or containment. Its primary function is to control the flow of liquid that passes through it, enabling the operator to regulate the amount and direction of liquid that is distributed or expelled. The valve typically comprises a movable gate or plunger that opens and closes against the flow of liquid, guided by a lever or other actuator mechanism.
This valve is commonly found in industries such as oil and gas, chemical processing, water treatment, and many others where precise control of liquid flows is critical. So, if you were wondering, “what does the internal liquid outlet valve do?” – it’s pretty clear that it plays an essential role in the efficient and safe operation of machinery that handles liquids.
Controls the flow of liquid out of a container
The function of a container’s liquid flow control is one that often goes unnoticed, yet it plays a crucial role in our daily lives. Imagine pouring a cup of coffee without a lid and without a well-designed spout. Chances are you’d end up with more coffee on your countertop than in your cup.
The same goes for dispensing liquid from a bottle or a jug. A well-designed flow control ensures a steady stream of liquid with minimal spillage. We use flow control mechanisms in products ranging from household items like kettles and pitchers to industrial-scale machinery, such as chemical reactors and water treatment centers.
The valve or spout used for controlling the flow of liquid can be manual or automated, depending on the application. Regardless of the type, flow control mechanisms help keep liquids in check and reduce waste, facilitating a cleaner, more efficient, and more affordable world. So, the next time you pour a drink or fill up a tank, thank the flow control mechanism for making it easy and clean.
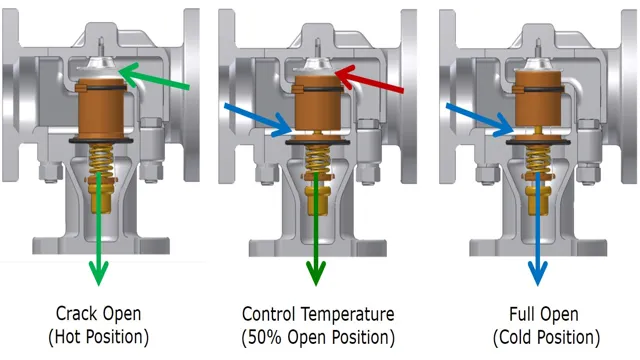
Prevents spills and leaks
When it comes to preventing spills and leaks, having a functional solution is crucial. It can save you a lot of hassle and time, not to mention prevent any potential damage or accidents from occurring. There are different methods and products you can use, but they all aim to achieve the same goal.
For instance, spill barriers and containment systems are designed to keep any hazardous materials and liquids within a certain area, preventing any potential spills or leaks from spreading. Additionally, spill trays and pans can help catch any spills or leaks that do occur, keeping them contained and preventing any further damage. Investing in these types of solutions can help you maintain a clean and safe workspace, while also adhering to environmental regulations and standards.
So, if you want to take a preventive approach when it comes to spills and leaks, it’s important to opt for functional and reliable solutions.
Regulates the pressure of the liquid
The function of pressure regulators in liquid systems is crucial for ensuring the proper flow of fluids for various applications. The primary task of a pressure regulator is to maintain a constant pressure of the fluid by controlling the flow rate. The regulator has an opening and a spring-loaded diaphragm that senses the pressure of the liquid.
If the pressure exceeds the set limit, the regulator reduces the flow rate by closing the opening partially. Similarly, if the pressure falls below the set limit, the regulator increases the flow rate by opening the valve further. Pressure regulators are commonly found in industries, such as oil and gas, water treatment, and chemical processing, where the safety and reliability of liquid systems are crucial.
In summary, pressure regulators play a vital role in preventing damage to pipelines and equipment by regulating the pressure and flow of fluids effectively.
Types
The internal liquid outlet valve is an essential component in many types of equipment that rely on liquid flow control. This valve functions by regulating the flow of fluid through a pipe or tubing system, ensuring that it flows in the right direction, at the correct pressure and rate. The internal liquid outlet valve is typically installed within the piping system and can be categorized into different types, such as ball or gate valves, check valves, globe valves, and butterfly valves.
Each performs a specific function and is designed to meet different flow control requirements. For instance, ball valves are typically used to regulate flow in high-pressure applications, while globe valves are best suited for low flow rates. By selecting the right type of internal liquid outlet valve, you can ensure that your equipment is operating at optimal performance and efficiency levels.
Ball valve
A ball valve is a type of valve that uses a ball to regulate the flow of fluids within a pipeline. There are several types of ball valves available on the market, including floating ball valves, trunnion-mounted ball valves, and rising stem ball valves. Floating ball valves are the most common type of ball valve, where the ball is free to move within the valve body.
They provide good sealing and are easy to operate, making them ideal for many applications. Trunnion-mounted ball valves feature additional support provided by the trunnions, which can handle higher pressure and larger size valves. These valves are suitable for high-pressure applications and are often used in the oil and gas industry.
Rising stem ball valves have a threaded stem that raises the ball to open or close the valve. They are commonly used in applications where fluid flow control is critical and require a durable and reliable valve. Overall, selecting the appropriate ball valve depends on the specific application and the flow control requirements of the system.
Butterfly valve
When it comes to controlling the flow of fluids in piping systems, butterfly valves are a popular choice due to their effective sealing mechanisms. There are four main types of butterfly valves: resilient seated, high-performance, triple offset, and double offset. Resilient seated butterfly valves are primarily used for low-pressure applications, as they feature an elastomer liner that provides a reliable seal.
High-performance butterfly valves, on the other hand, are designed for high-pressure applications and feature a metal or graphite seat. Triple offset butterfly valves offer even better sealing capabilities, thanks to their conically tapered disk seating against a metal seat, making them ideal for corrosive or abrasive materials. Lastly, double offset butterfly valves are suitable for high-temperature applications, as they feature an eccentric design that minimizes seat wear and offers a tight seal.
Whichever type of butterfly valve you choose, it is essential to ensure that it is suitable for your application’s specific requirements.
Gate valve
Gate valves are versatile valves that can be used in a variety of applications, and they come in different types. One type of gate valve is the rising stem valve, which is easily identifiable by its stem that rises as the valve is opened and lowers as the valve is closed. This type of valve is ideal for applications with limited space as it can be easily installed in tight spaces.
The second type of gate valve is the non-rising stem valve, which is ideal for applications where there is limited vertical space. In this type of valve, the stem does not rise as the valve is opened, but instead, it rotates in a horizontal plane. This type of valve is also ideal for applications that require frequent operation as it is less susceptible to damage compared to the rising stem valve.
Ultimately, the type of gate valve chosen will depend on the application requirements, so it’s essential to consult an expert to ensure the right valve is selected for the job.
Globe valve
Globe valves are known for their excellent throttling and control properties and are widely used in a variety of industries for regulating fluid flow. There are various types of globe valves available in the market, each designed to suit specific applications and needs. One common type of globe valve is the cast-iron globe valve, which is ideal for controlling water flow and other non-corrosive fluids.
For applications that involve corrosive fluids, the cast steel globe valve is the go-to option due to its high resistance to corrosion. Another widely used type is the bronze globe valve, which is most commonly used in fire protection systems and marine applications. Stainless steel and PVC globe valves are also available and are used in industries ranging from pharmaceuticals to food processing.
Each type of globe valve has its own set of advantages and limitations, making it important to choose the right type for the intended application.
Applications
The internal liquid outlet valve is a crucial component of many fluid control systems, as it allows for accurate and precise control of liquid flow rates. This valve is typically designed to be located within a fluid handling device or system to allow for quick and easy access to the flow of liquid. The valve functionally controls the flow rate of liquid passing through it, which is crucial for various applications such as chemical processing, water treatment, and many types of industrial manufacturing.
In addition to being highly customizable based on the application, the internal liquid outlet valve is also very reliable, durable, and easy to maintain. With its robust design and ability to handle a wide range of liquid types, this valve is the perfect solution for all of your fluid control needs.
Food and beverage industry
In the food and beverage industry, there are numerous applications that businesses can take advantage of in order to enhance their operations. One such application is inventory management software, which can help handle the complexities of managing the ingredients and supplies that are necessary for food and beverage production. Not only does this software help with ordering and stocking, but it can also track expiration dates, provide alerts for low quantity levels, and generate reports to help with budgeting and forecasting.
Another useful application is point of sale (POS) systems, which allow businesses to process transactions quickly and securely while also providing data on sales volume and customer behavior. This data can be used to make informed decisions about pricing, promotions, and menu offerings. By using these applications, businesses in the food and beverage industry can improve their efficiency, accuracy, and profitability.
Pharmaceutical industry
The pharmaceutical industry has a wide range of applications that impact the health and well-being of people worldwide. One of its primary applications is the development and manufacture of drugs that treat a variety of medical conditions. From antibiotics to antidepressants, pharmaceutical companies are responsible for bringing life-changing medications to the market.
Additionally, the industry is responsible for the development of new vaccines that can help prevent the spread of diseases. Furthermore, the industry plays a significant role in drug delivery systems, including pills, injections, and transdermal patches. These delivery systems are designed to ensure that the medication is absorbed properly into the patient’s system, providing the most effective treatment.
Overall, the pharmaceutical industry is instrumental in advancing medical research and improving the quality of healthcare for people around the world.
Conclusion
In conclusion, the internal liquid outlet valve is like the unsung hero of the plumbing world. While it may not get as much attention as other components, it plays a crucial role in regulating the flow of liquids and ensuring that everything runs smoothly. Think of it like a traffic cop directing the flow of cars, except it’s directing the flow of your liquids.
So, the next time you turn on your faucet or use your plumbing system, remember to thank the internal liquid outlet valve for its unsung service.”
FAQs
What is the main purpose of the internal liquid outlet valve?
The internal liquid outlet valve controls the flow of liquid out of a container or system and prevents leaks.
How does the internal liquid outlet valve work?
The valve uses a mechanism to open and close the outlet, allowing or stopping the flow of liquid.
Can the internal liquid outlet valve be replaced if it stops working?
Yes, the valve can be replaced either by a professional or by someone with technical knowledge of the system.
Is it important to maintain the internal liquid outlet valve?
Yes, regular maintenance of the valve ensures proper functioning and prevents potential leaks or malfunctions.
Are there different types of internal liquid outlet valves available?
Yes, there are various types of valves available for different types of systems, including ball valves, gate valves, and globe valves.